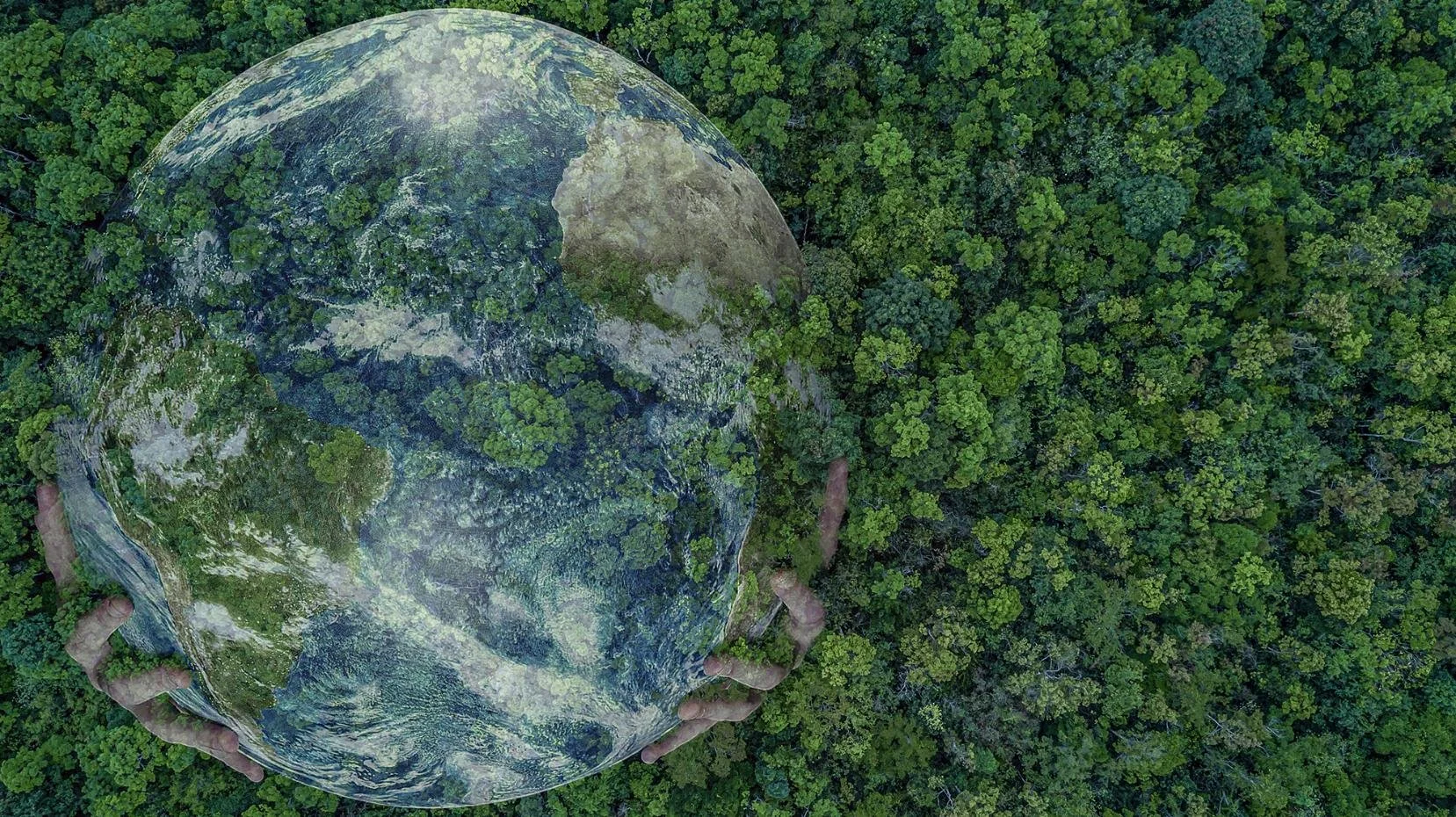
RGC BUILDING A SUSTAINABLE FUTURE
Experience the innovative difference of a Real Green Concrete OPC-free binder.
WHAT IS REAL
GREEN CONCRETE?
Concrete produced from Real Green Concrete “RGC” binder is exactly that. Our binder contains no Ordinary Portland Cement (OPC).
RGC BINDER AND
ENVIRONMENTAL MISSION
RGC binder uses industrial by-products and wastes to reduce landfill impact and significantly cut carbon emissions from traditional OPC production.
INNOVATIVE FORMULATIONS
FOR CLIMATE IMPACT
Our patented binder formulations offer substantial potential for climate change mitigation by lowering Global Warming Potential (GWP) by at least 68% compared to OPC.
BENEFITS OVER OPC
Recent trials show that RGC binder requires a minimum of 10% less cement, results in 5% lighter concrete, and uses less water, making it environmentally and economically advantageous.
FLEXIBLE PERFORMANCE
AND FAST SETTING
RGC binder offers flexible setting times tailored to project needs, with the ability to achieve initial strength rapidly for mould striking in as little as 8 to 10 hours.
ENVIRONMENT IMPACT
Utilising RGC binder not only reduces environmental impact but also enhances construction efficiency and sustainability, contributing positively to climate change efforts.
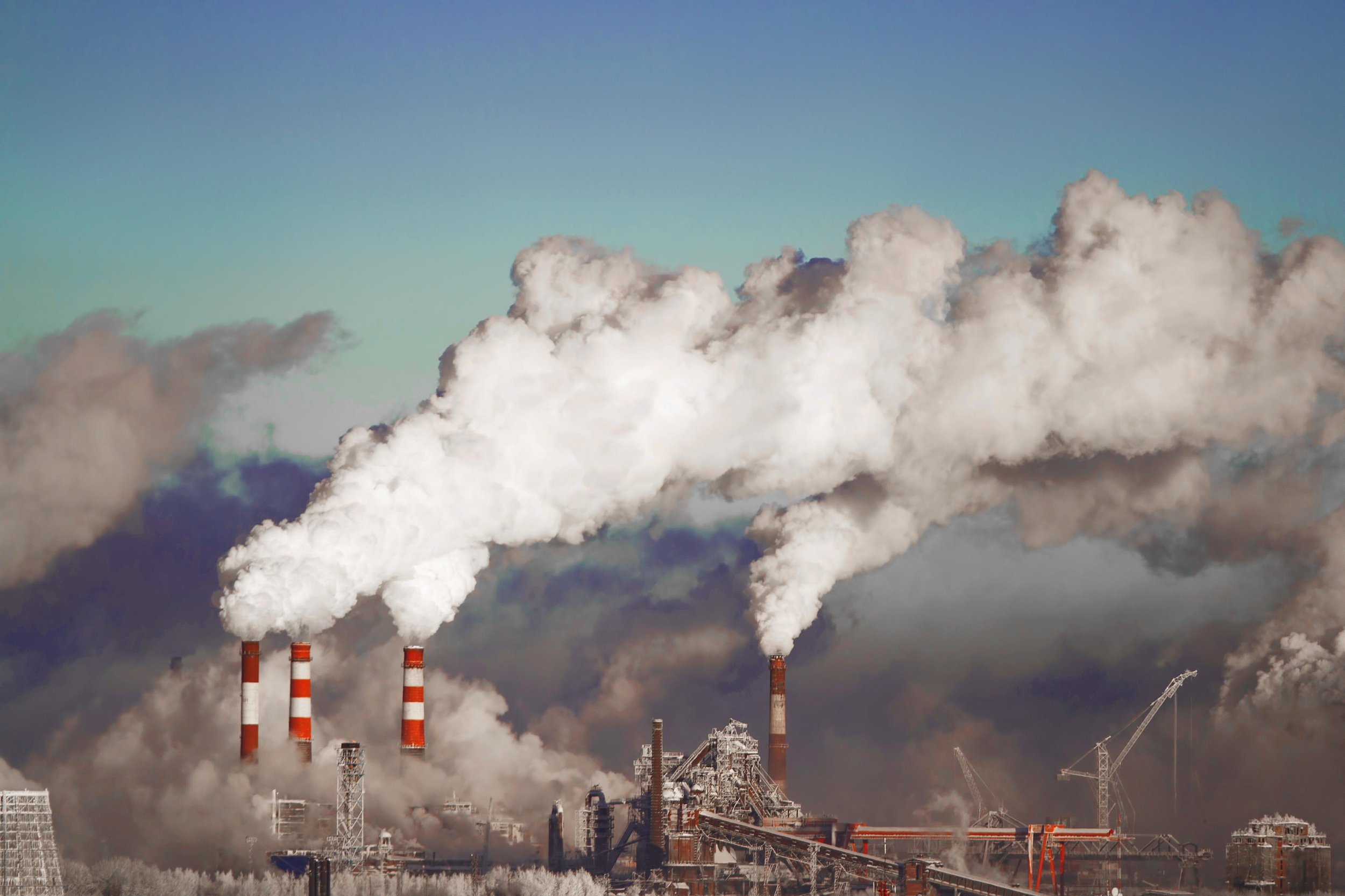
WHY IS OPC SO HARMFUL?
Although Ordinary Portland Cement (OPC), the current main ingredient in concrete, has been instrumental in helping shape our built environment, it does leave a substantial carbon footprint.
It is widely acknowledged that cement production contributes a massive 8% to the world’s CO₂ emissions – 3 times more than the whole aviation industry. If cement were a country, it would be the third biggest source of emissions after China and the USA.
2.2 BILLION
tonnes CO₂
In 2016, the cement industry produced 2.2 billion tonnes of CO₂.
8% Global
CO₂ emissions
Just from one industry, cement production.
Concrete is the most widely used
man-made material in existence. It is second only to water as the most-consumed resource on the planet. Production is forecast to grow by as much as 38% by 2050 if no intervention is made.
Our mission is to provide a solution for intervention and climate change mitigation. Our patented binders not only contain ZERO OPC but also use by-products and wastes sourced from industries that would otherwise go to landfills. We have thus created products with at least a 65% lower Global Warming Potential (GWP) compared with OPC.

OUR BINDER APPLICATIONS
Our innovative RGC binders can produce a range of concrete grades suitable for diverse industries and applications.
Since RGC binder-based concrete relies on a chemical bonding process, we have been able to tailor the chemical composition to excel in various applications. Whichever properties are required, such as high strength, high permeability, shock absorption, conductivity, water durability, or rapid setting, our binders have you covered.
READY MIXED CONCRETE
REINFORCEED
CONCRETE
HIGH PERFORMANCE
CONCRETE
WORKABLE
CONCRETE
HIGH STRENGTH FLEXIBLE CONCRETE FOR MULTIPLE APPLICATIONS
PERVIOUS
CONCRETE

OUR HISTORY
Real Green Concrete is
the invention of Dr. Aissa Bouaissi, an expert in cementitious materials.
With experience in academia and industry, he discovered a chemical process that triggers the hardening of the mixture through activation rather than the crystallisation and hydration typical of OPC. His patented technology can be readily adjusted to suit various concrete applications.
Because it relies on a chemical reaction, both liquid and powder chemical forms can be used to activate the binders, allowing for a wide range of materials to be incorporated into the matrix, making the best use of those that are locally available. No special equipment is required – RGC binders are a “drop in” solution for existing OPC users.
VISION AND
VALUES
Our vision is to bring a new material
to the Construction Industry that significantly lowers its carbon footprint
by providing an OPC-free solution to
the sector.
The production of OPC generates carbon-based pollution three times higher than the total emissions from global aviation annually. While we do not anticipate a complete halt in OPC production worldwide, increasing awareness of a carbon-efficient alternative in construction across more countries can significantly contribute to reducing global environmental harm.
Sea levels are rising, flooding is an increasing problem, and the Environment Agency (EA) has committed to achieving carbon neutrality by 2030. There is a demand for fast-setting products to be employed in tidal and river environments. Our products’ outstanding resistance to acid/alkaline attack and chloride diffusion will provide significant benefits.
Precast work in the form of bridges, sewers, cladding, retaining walls, paviours and specialist items like staircases, beams, and floors need a rapid hardening, high-strength concrete that is competitively priced. Currently, moulds are generally turned around in 24 hours. The use of RGC can double production without heat to aid the process.
CONTACT US
If you’d like to contact us about Real Green Concrete or to learn more about our products, please contact us. You can call our office or fill in our contact form with details of your enquiry. We look forward to hearing from you.
info@realgreenconcrete.com
01752 697000